QA Consultants Saved a Large Electrical Utility Approximately $85 Million
Abstract
QA Consultants helped a large electrical utility serving over 700,000 customers to modernize and automate its work order processing, resulting in approximately $85 million in savings. The utility faced challenges with inefficiencies and inaccuracies in its work order creation process, which hindered performance operations. QA Consultants implemented a solution using the MicroFocus/HP UFT Test Automation Platform, streamlining the process, reducing human error, and allowing faster, automated test cycles. As a result, the processing time for work orders was reduced from 4 hours to 1 hour, and the system was enhanced to handle peak loads and concurrent operations. This automation led to significant operational efficiencies and cost savings for the utility.
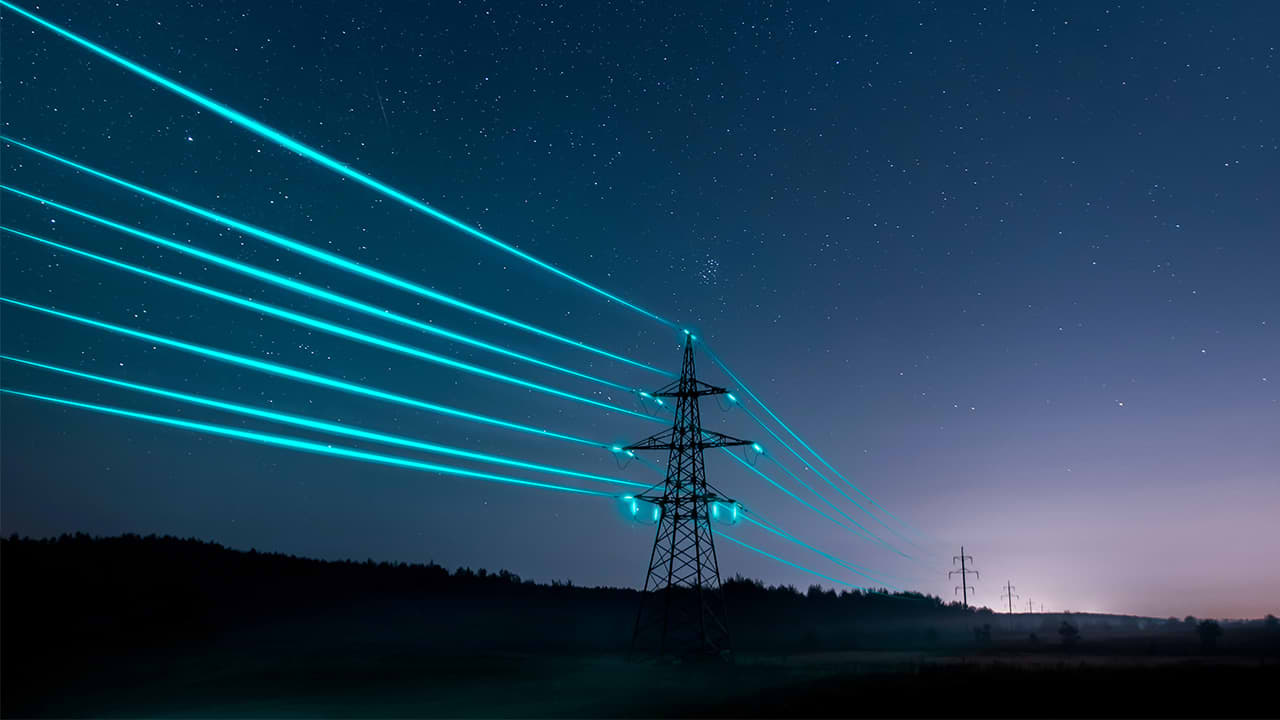
At a Glance
A large electric distribution company that services more than 700,000 customers needed to process its work orders faster and more accurately.
The Challenge
Inefficient work order processing needed to be modernized with automation. The utility aimed to generate faster work order creation to support its performance operations. Accurate test data was required to meet the QA program’s aggressive schedule and frequent iteration test cycles.
The Solution
Our team upgraded the work order creation process with the MicroFocus/HP UFT Test Automation Platform. This approach significantly reduced the time required to generate the test data. It also eliminated human error that required corrections. The new installment enabled repeated automated runs to support multiple test runs, test cycles, and test phases.
The Results
After QA Consultants completed a SAP-based MRP installation, the system could successfully support peak loads.
The Performance Stress Testing run that processed 80-100 work orders was reduced from 4 hours to 1 hour. The installation was also able to support concurrent executions on multiple machines. The results were significant savings for the power company.